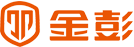
本报记者 蒋新会 李权 张雷
7月1日,金彭黄金动力2.0超高速系列正式发布。该系列采用全新的“动力心脏”——矢量磁阻智能动力系统,转速扩展可达10000转,最高系统效率93%,电机综合故障率降低80%以上,速度可达65KM/H。
“不仅在行驶速度上突破了行业技术‘天花板’,更推动电动三轮车动力系统进入智能化新时代。”金彭电三产业平台主王海冲说。
技术革新的背后,是江苏金彭集团发展新质生产力的持续探索。
党的二十届三中全会《决定》提出,以国家标准提升引领传统产业优化升级,支持企业用数智技术、绿色技术改造提升传统产业。拥有20年历史的江苏金彭集团,积极推动科技创新、智改数转,紧抓风口,一路向“新”,在高质量发展道路上破浪前行。
创新引领
创新是引领发展的第一动力,唯有不断创新,才能立于不败之地。坚持技术创新,成为金彭发展新质生产力的“最大增量”。
从2009年到2024年,加入金彭15年间,现任金彭集团党委委员、科技专利部总监的朱红军可以说是金彭产品从“土特产”到“高大上”的亲历者。
“金彭科技的发展可以用日新月异来形容。”朱红军感慨地说。1000余项专利技术,300余件商标保护,从20余人扩展到现在500余人的专业研发团队,行业内第一家博士后创新基地,2013年获得电动摩托车生产资质,2017年获得国家CNAS实验室认可,2018年参加三轮电动车国家行业标准的制定,2019年拿到新能源高速车生产资质,电动三轮车行业第一家获得“江苏精品”认证的企业,行业内唯一一家获得全品类生产资质的企业,2019年又拿到中国驰名商标称号……朱红军说起金彭科技的前进历程,黝黑的脸庞上露出开心和自豪的笑容。
作为技术人才,朱红军加入金彭后,迅速投入金彭生产标准化体系的建立和制定,从基础制造技术开始突破,图纸、工艺流程、操作流水线,到整车生产的体系化、标准化、通用化,从焊接技术的创新、车体一体化冲压成型,到行业首创一体边梁技术……“金彭连续16年行业内第一,技术上的领先,绝对不是吹的。”朱红军笑着说。技术的进步不仅带来质量的提升,更增加了金彭的生产效率,这也是金彭在行业内遥遥领先的底气。
最近几年,朱红军和金彭的技术团队致力于新能源电动车等科技项目的研发,其主持的新能源低速电动车项目通过省、市科技鉴定,技术水平国内领先,不断引领行业产品及技术的发展,多项科技项目获得省市科技成果奖,多项技术获得国家发明专利。其中,油电混合动力技术获得独有核心专利技术,运用该技术的新能源电动车获得江苏省机械工业科技进步奖一等奖、江苏省专利奖新产品奖、徐州市专利奖;研发的新能源电动车项目获得徐州市科技计划项目,其产品技术获得江苏省科技进步奖二等奖、江苏省专利奖新产品奖、徐州市科技进步奖等荣誉。
“科技是企业的生命,只有在技术上不断创新,在品质上精益求精,才能推动企业高质量快速发展。”朱红军说。
技术革新
一辆电动三轮车的“动力心脏”,如何实现蜕变?
“对于用户来说,电动三轮车动力系统的常见故障是‘烧机’。‘烧机’一般烧两个部分——磁钢或霍尔。同时,‘超越时速50公里’也存在较多的技术难题。”金彭电三产业平台技术中心总经理王迪光说,“我们集团一向鼓励以用户需求为核心进行技术创新,我们当时就想向这两大难题‘宣战’。”
磁钢和霍尔是什么?有什么作用?通俗地讲,电机中的磁钢产生磁场,与电流相互作用,从而产生转矩驱动电机转动;霍尔是一种对磁性敏感的电子元件,通过霍尔传感器感知磁场的变化,可以控制电机的速度,从而实现电动车速度的调节。
怎样才能弥补原有动力系统的短板呢?尝试过多套方案后,王迪光和团队发现,只进行简单的改造,治标但不治本。
来自浙江宁波的王迪光,2022年经同事介绍来到金彭工作,此前曾经在汽车行业技术研发领域深耕多年。
为何不能把汽车动力系统技术应用到电动三轮车上,将磁钢和霍尔全部“删除”,来个“釜底抽薪”?
转变思路后,经过数百次的失败、调试、改进,矢量磁阻智能动力系统成功面世——高效率、高转速、低故障,动力更强、载重更多、操作更便捷,续航里程更多,时速更是突破了50公里。
不仅如此,该系统还将传统的三项矢量控制器升级为六项矢量智能控制器,能够支撑更为强大的运算性能。这意味着,电动三轮车上也可以植入人机交互系统、车载娱乐系统等,实现车辆轨迹记录、健康数据监测等功能,让电动三轮车动力系统进入了智能化新时代。
创新无止境。如今,金彭电三产业平台技术中心拥有近50人的研发团队,平均年龄不到30岁。他们把电动三轮车的爬坡耐久时间从4至6分钟提高到15分钟,是行业平均水平的两到三倍,他们将天幕装配到电动三轮车顶部,持续吸收太阳能进行充电,每日续航里程可增加二三十公里……
在金彭旗下江苏中玻玻璃科技有限公司的生产车间,成堆的天幕成品整装待发,一块块黑色光伏电池片在弧形玻璃的加持下科技感十足。自动化生产线上,从预处理、上片、切片到打磨、锻孔等流程,实现自动化生产,自动化程度达到70%。
这家位于徐州工业园区的企业成立于2021年,起初只有总经理李冬冬1人。“建厂前考察了方圆1000公里内的20多家玻璃生产厂家。那时候一天工作十二三个小时是常事。”90后李冬冬说,“经过3年的发展,公司目前已经拥有两个厂区、140多人,产品供应北汽、江淮、奇瑞、中联重科、徐工等企业,远销美国、沙特、泰国等多个国家。”
令李冬冬至今记忆最深刻的是2022年三四月份的一天。为了保证吉麦新能源一个车型的顺利量产,他带领团队36个小时连续攻关,不断调整工艺流程,最终将后挡玻璃的厚度从4-5毫米压减到3.2毫米,且所有指标达到指定的标准。“我们不断进行工艺创新、流程创新,提升智能化、自动化水平,生产效率持续提升。”李冬冬说。
数智力量
一滴水,也能降本增效?
通过数字化能源管理系统,针对冲、焊、涂、总四大车间进行工序级能源管控,实现针对水、电、气的采集、监控、分析、调度、优化。金彭集团数字化中心总监赵光说:“这些看似不起眼,实际降本增效空间很大。”
走进江苏吉麦新能源车业有限公司(以下简称“吉麦新能源”),数智化转型正改变生产全过程——研发设计更高效。通过市场洞察确定产品定位,应用数字孪生、虚拟仿真、三维建模等技术设计整车,利用3D打印技术打印整车。“从信息采集到设计研发,大多数过程通过电脑完成,可以极大地降低成本、提升效率。”赵光说。
生产过程更智能。12台ABB机械臂忙到“飞起”,实现冲压、涂装环节的智能化生产。以前需要20多名工人合作才能完成的冲压流程,现在仅需3名工人。50多台焊接机器人分组配合,对冲压成型的钢板进行焊接。30多台智能AGV小车,根据设定的参数自动配送物料。通过感应识别车辆身份识别码(VIN),系统就会自动调整至相应的生产模式,满足用户的个性化需求。“从第一道工序到总装完成下线,平均3分钟就可以下线一台新能源电动汽车。”吉麦新能源法规认证总监梁承志自豪地说。
生产管理可视化。库存数量、在制品总量、发货量、焊装下线量、涂装下线量、总装下线量等数据即时更新,在电子显示大屏和管理人员手机终端上一目了然。“无论哪个生产环节、哪道工序、哪个工位出了问题,都可以通过手机终端下达指令进行调整。”梁承志说。
市场服务更精准。轻点鼠标,所有联网车辆实时运行状态随时呈现。吉麦新能源建立车联网平台,所有售出的车辆全部动态接入平台。发现运行故障,系统会自动向用户发出警示提醒信息。
日前,吉麦新能源“用户驱动下全周期全流程全要素新能源汽车智能制造工厂”,成功上榜江苏省智能制造示范工厂。包括此前获得的江苏省智能示范车间、江苏省企业五星级上云企业、徐州市产业数字化转型示范试点企业等,一个个荣誉记录着企业“智改数转”的发展历程。
“智改数转”是企业提质增效、抢占发展制高点的关键之举,也是推进制造业转型升级、实现高质量发展的必由之路。
自2020年4月20日首款新能源汽车凌宝BOX正式下线以来,目前吉麦新能源共有凌宝BOX、凌宝COCO、凌宝Uni三款纯电动乘用车和国吉大象两款纯电动货车,其中凌宝BOX车型已成为A00级新能源电动汽车销量前五车型。
除了聚力打造智慧工厂,先后建成智慧总装工厂、智能涂装工厂等信息化、智能化建设项目,吉麦新能源还通过构建工业互联网平台,打通企业MES系统、能源管理系统、安全环保管理等,将公司内全业务上“云”,实现企业数据流、业务流、管理流等各业务数据在线互通共享、可视化展示,真正实现“制造”向“智造”转变。
“目前智能车间的综合效益显著提升,人员产量比率下降50%、合格率提升至90%,能源利用率提升40%。”赵光说。
紧抓风口
站在风口,才能御风飞翔。
“锂电产业就是一个新风口。随着国家相继出台锂电池的强制标准和法规,尤其磷酸铁锂的价格一跌再跌,成本已经接近铅酸电池,为锂电产业发展提供了重要条件。”金彭电三产业平台锂电事业部总经理陈雷坚定地说,2023年磷酸铁锂行情一路向下,最高点是年初的16.6万元(吨价,下同),最低点是年底的4.6万元,全年跌幅72.29%,可谓“膝盖斩”。
其实早在2015年,金彭就确立了“锂电”的技术发展方向,而真正推动电动三轮车锂电化的落地,要从去年说起。去年7月,陈雷跟随金彭集团董事长鹿守光到南方考察市场,发现当地低速电动车锂电的使用率很高,但是锂电的生产规范化还存在隐患。
“同等体积,锂电池储能是铅酸电池的3倍,使用寿命是铅酸电池的3-5倍,而价格仅比铅酸电池略高。而且锂电池更环保,回收率可以达到99.9%。”对于锂电的优势,陈雷如数家珍,“锂电化还是实现产品智能化的基础,我们自己的产品实现锂电化,必须选择安全性能可靠的电池。”
于是推动金彭电动三轮车锂电化提上日程,锂电事业部应运而生。
市场上的电池产品林林总总,选择哪一种呢?经过低温、高温、穿刺等多次测试,综合考虑安全性能和成本等因素,金彭最终选择了磷酸铁锂电池。
如今,占地4000平方米的锂电生产车间已经投产。走进生产车间,只见工人们正在生产线上忙碌,一个个刚刚下线的锂电PACK(集成包)正在接受严格的充放电测试。
“我们与比亚迪、多氟多、科信等企业强强联合,PACK全部采用A级电芯。目前共有3条生产线,上个月生产18000组,这个月有望达到4万组。”陈雷信心满满,“准备新建一个锂电产业园,建成后年产值可达20亿元。今后还将向无人机、无人车电池配套方面拓展。”
你见过巨型“锂电池”——储能柜吗?由吉麦新能源全资子公司江苏金派克新能源有限公司生产的储能柜,长12.2米、宽2.4米、高2.9米,一般供往三峡大坝、国家电网等,用于储存电能。“该储能柜项目去年做了600兆瓦时(注:1兆瓦时=1000千瓦时),年产值约8亿元。”该公司总经理汤克说。
“我们在淮北的生产车间有一条自动化生产线,电芯的堆叠、焊接、视觉检测等环节,都实现了自动化生产。还有一个占地100亩的新厂区正在建设,准备建设PACK生产线和废旧锂电拆解线,不久后即将投产。”
一辆高速行驶的动车上,每节车厢装有8块电池包,随时为动车提供备用电源。这些正在测试阶段的动车电池包,也是由江苏金派克新能源有限公司研发生产。“如果顺利达产,可创造10亿元以上的产值。”汤克说。
“用科技创造美好出行 以创新驱动企业成长”,金彭初心不改;致力于“成为全球轻型绿色交通工具领导者”,金彭目标坚定。
坚持创新驱动、技术赋能,加快培育新质生产力,金彭向新而行,向高而攀,向智发力,一路领跑。